限位开关及限位测量方法
测量原理
功能
应用
VEGA 限位开关有哪些优点?
限位开关可以应用在哪些地方?
限位开关在过程工业中的典型应用有:
- 过程容器
- 储罐
- 料仓
- 管道
- 溢流池
限位开关在这些应用中可用作:
- 满料检测或溢流防护装置:开关命令控制是否停止装料
- 空载检测:开关命令控制是否开始装料
- 泵类防干运转保护器
- 泄漏监测
- 油水界面检测
- 泡沫检测
- 界面检测
限位开关多用于以下待测介质:
- 液体
- 膏体
- 轻型固料,如水泥、面粉等
- 重型固料,如砾石、碎石等
- 泡沫
限位开关必须满足哪些要求?
产品生产和加工的最终目标是保持恒定的产品质量。为了实现这一目标,每个行业对所用的测量仪表也会提出各种各样的高要求。VEGA 可为每种应用场合提供合适的限位开关。
如选择特定测量原理和仪表配置,VEGA 限位开关也可用于以下领域:
- 防爆区域和最高等级至 SIL2 的安全设备
- 具有化学腐蚀性的介质
- 具有磨损性或粘附性的介质
- 食品及制药行业中的卫生应用,可提供经过认证的材料及过程连接
- 极端的温度和压力条件
探索限位开关在您的行业内有哪些用途
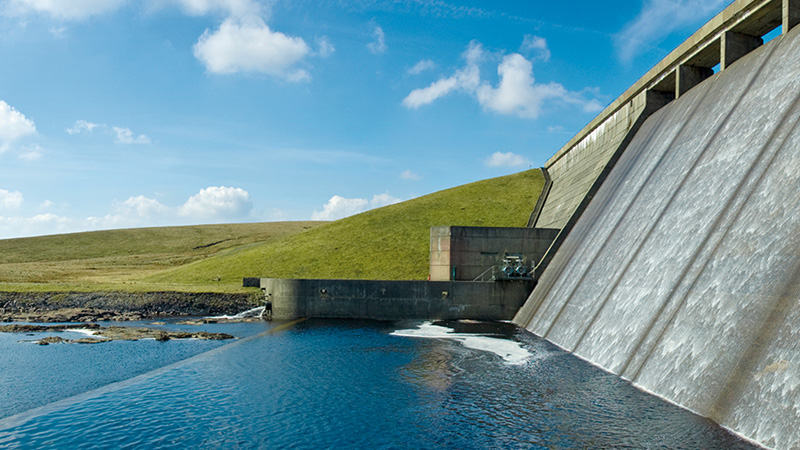
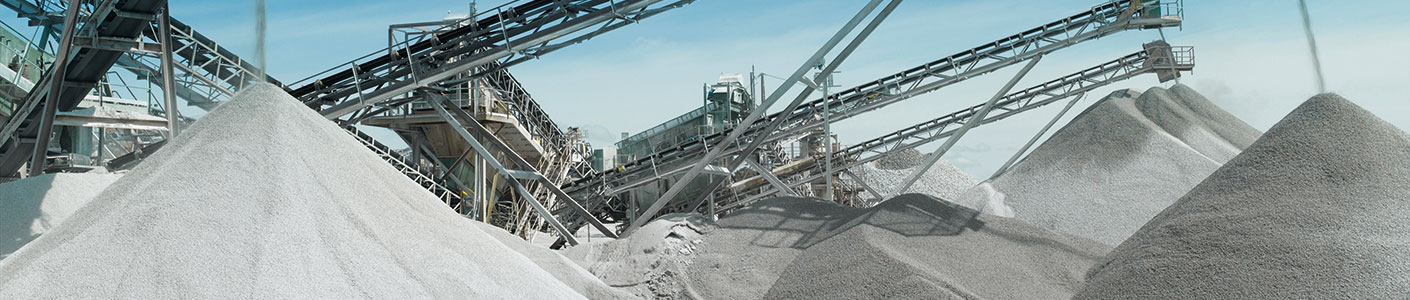
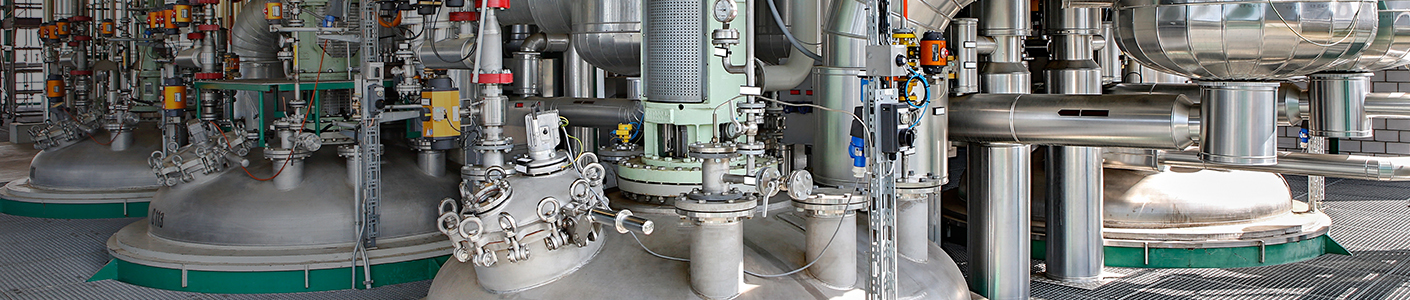
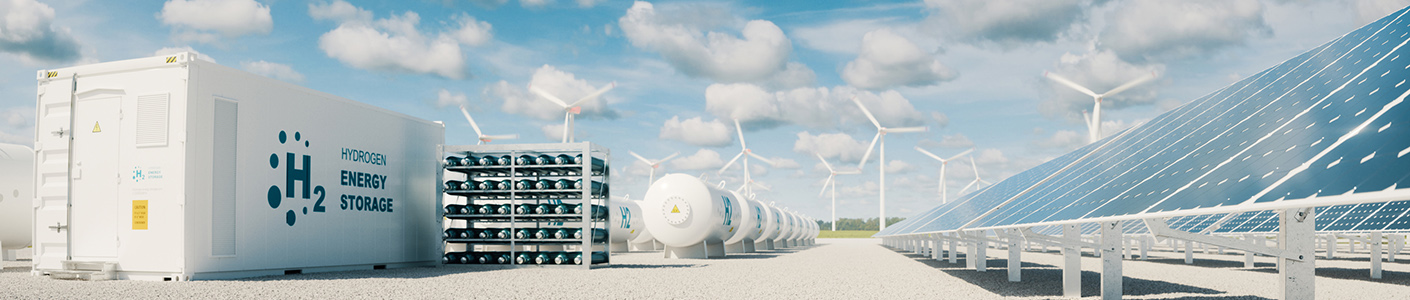

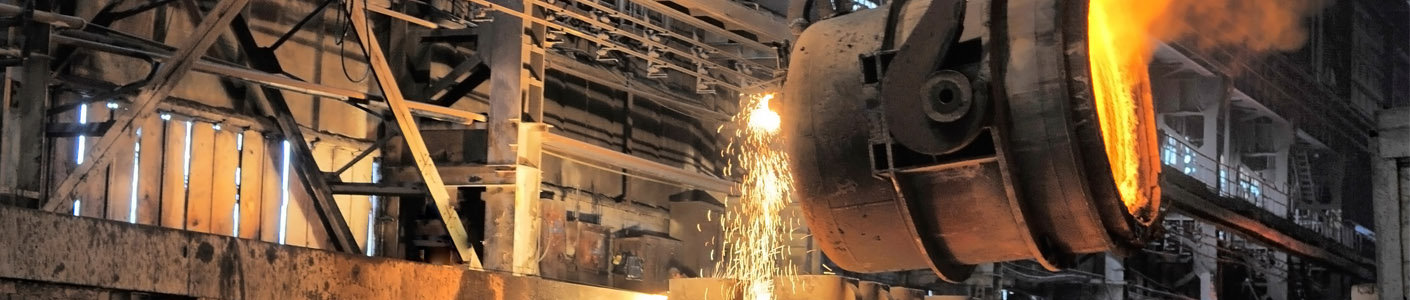
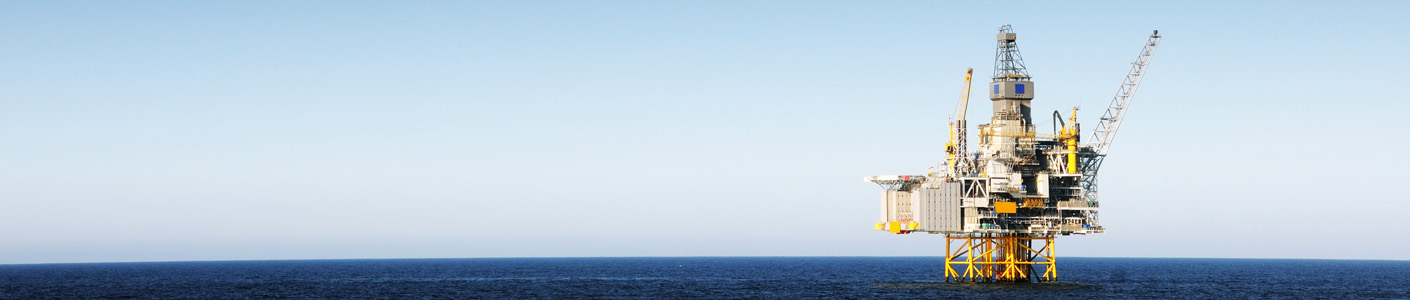
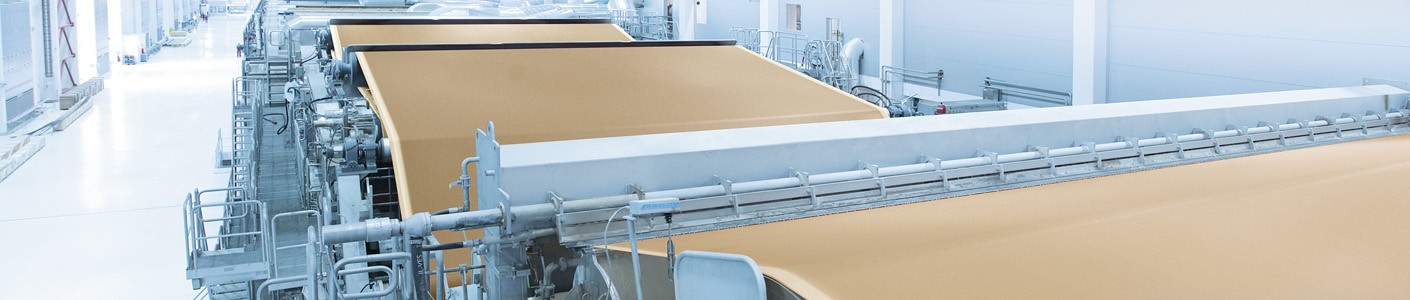
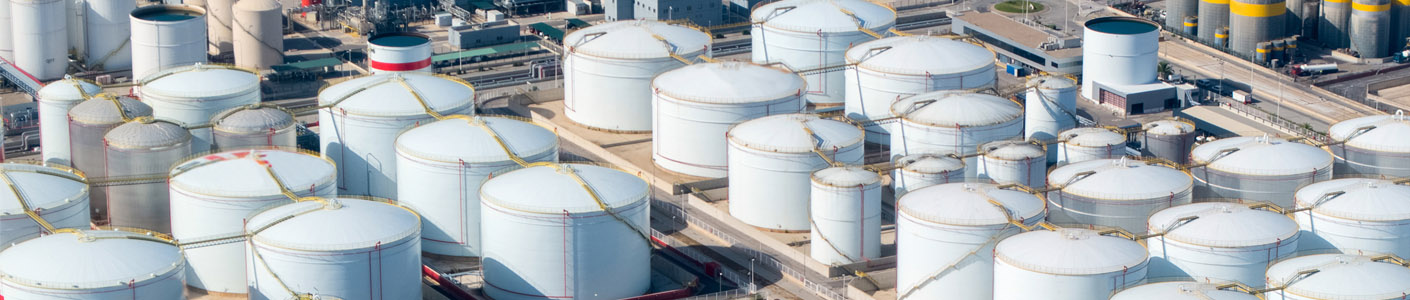
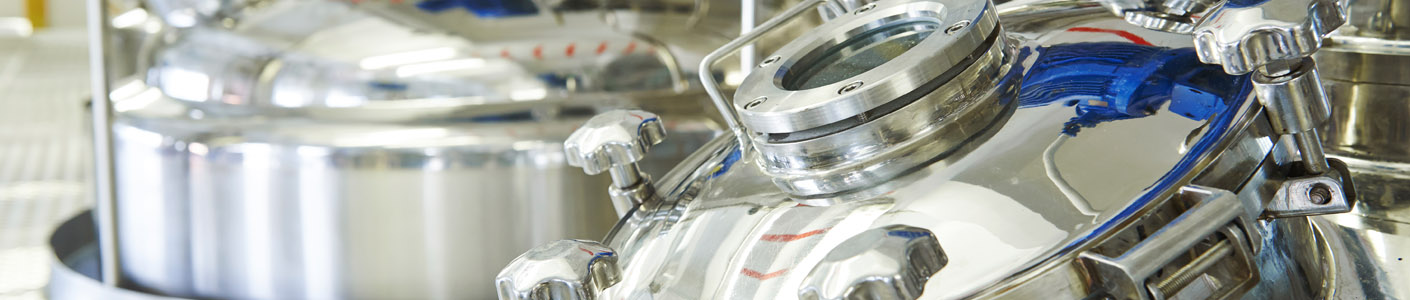
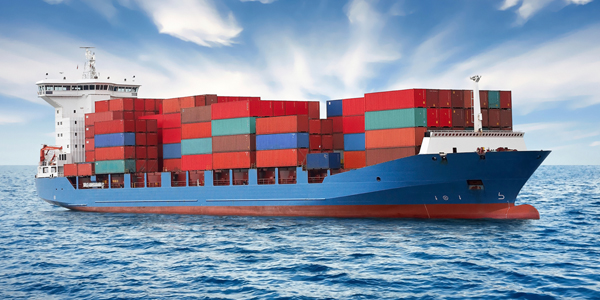
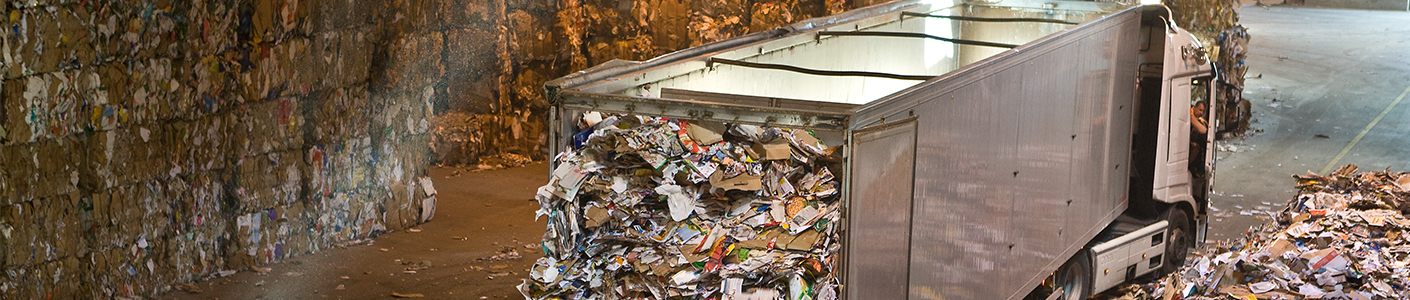
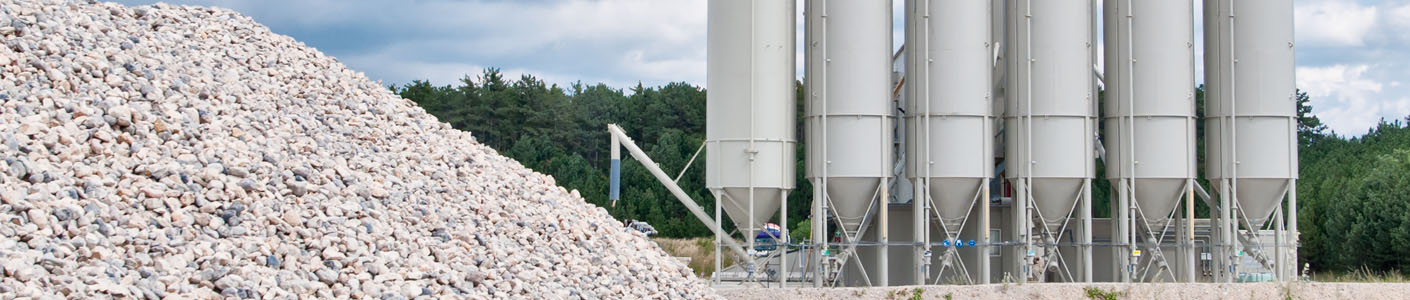
关闭